Why Nichrome Wire Reigns Supreme in Heating Elements
For anyone working with resistance heating, one material consistently comes to mind: Nichrome wire. But what makes this alloy, primarily composed of nickel and chromium, the undeniable star in applications ranging from industrial furnaces to everyday toasters? The answer lies in its unique combination of properties and advantages, making it perfectly suited for efficiently and reliably converting electrical energy into heat.
The Core Strengths of Nichrome Wire
1. High Resistivity for Efficient Heating
At the heart of Nichrome's effectiveness is its high electrical resistivity. This fundamental property means Nichrome inherently resists the flow of electric current, and this very resistance is what generates heat. Unlike highly conductive materials such as copper, which allow current to pass with minimal energy loss, Nichrome converts a significant portion of electrical energy into thermal energy. This characteristic not only boosts energy efficiency but also allows for smaller and lighter heating elements, making it the preferred choice for devices like ovens, kilns, and electric furnaces.
2. Exceptional Oxidation Resistance
Heating elements often operate at high temperatures and are exposed to air, which can lead to oxidation and degradation over time. However, Nichrome forms a dense, protective chromium oxide (Cr₂O₃) layer on its surface when exposed to high temperatures. This passivation layer adheres stably to the material, resisting peeling even above 1000°C, significantly extending the material's oxidation resistance and lifespan. This superior property makes Nichrome ideal for applications like electric furnace wires and heaters that are constantly in high-temperature, air-exposed environments.
3. High Melting Point for Extreme Temperatures
Many heating applications demand materials that can withstand extreme temperatures without deforming or failing. Nichrome's high melting point is a critical advantage here. This characteristic ensures that the wire remains stable and structurally sound even under intense heat, making it suitable for high-power applications where other materials might melt or soften. This reliability at high temperatures contributes to the safety and longevity of heating equipment.
4. Excellent Resistance Stability
When materials are heated, they tend to expand. Excessive thermal expansion can cause stress, deformation, or even breakage in heating elements, especially in applications with repeated heating and cooling cycles. However, Nichrome's resistivity exhibits minimal fluctuation at high temperatures, with an extremely low rate of resistance change. This means it delivers consistent heating effects and stable power over long periods, without significant power drift due to temperature increases, thereby ensuring the reliability and control precision of the equipment.
5. Good Ductility for Versatile Applications
While Nichrome wire's primary role is heat generation, its easy manipulation is a significant advantage. Nichrome boasts excellent ductility and workability, allowing it to be processed into various shapes—such as wires, strips, rods, and tubes—through drawing, rolling, and welding. Whether you need intricate heating filaments or large structural components, Nichrome can be flexibly customized to meet the assembly requirements of different devices.
6. Strong Corrosion Resistance
Beyond high-temperature oxidation, Nichrome also demonstrates robust resistance to chemical corrosion, maintaining good stability in alkaline and certain acidic environments. This makes it suitable for use in more aggressive industrial settings.
7. Cost-Effective and Economically Sound
Compared to other high-temperature alloys or precious metals (like platinum or molybdenum wire), Nichrome offers lower raw material costs and abundant reserves. Its mature processing technology allows for easy mass production. This combination ensures that the product delivers excellent performance while significantly reducing manufacturing costs, leading to higher profit margins.
Typical Nichrome 80/20 Parameters
Parameter | Value |
---|---|
Composition | 80% Nickel, 20% Chromium |
Max. Operating Temp. | ~1200 °C (2190 °F) |
Melting Point | ~1400 °C (2550 °F) |
Density | 8.4 g/cm³ (0.304 lb/in³) |
Resistivity | 1.09 Ω·mm²/m (650 Ω·circ mil/ft) |
Tensile Strength | 700-900 MPa (100-130 ksi) |
Thermal Conductivity | 11.3 W/(m·K) |
Thermal Expansion | 17 x 10⁻⁶ /°C |
Note: These values are typical for Nichrome 80/20. Specific properties may vary slightly based on manufacturing process and exact alloy composition. Please contact us for detailed specifications for your application.
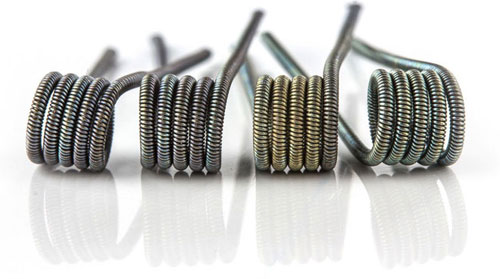
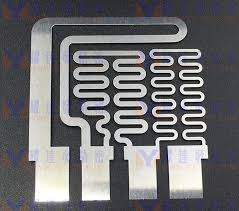
Nichrome Wire vs. Other Heating Elements: Why It Stands Out
While Nichrome wire is often the go-to for heating applications, it's helpful to understand how it compares to other common materials. Each alloy has its strengths, but Nichrome's unique balance of properties often gives it an edge:
- Iron-Chromium-Aluminum (FeCrAl) Alloys: FeCrAl alloys generally have higher operating temperatures and excellent oxidation resistance, sometimes even surpassing Nichrome in certain environments. However, they tend to be more brittle, especially after prolonged high-temperature use, making them less ductile and harder to form into complex shapes than Nichrome. Nichrome also generally offers better creep resistance and less sag at high temperatures.
- Copper and Silver: These metals are excellent electrical conductors but have very low resistivity, meaning they generate minimal heat when current passes through them. They are unsuitable for heating elements where significant heat generation is required.
- Carbon Fiber: Carbon fiber heating elements offer rapid heating and flexibility, often seen in infrared heaters or specialized applications. However, they typically operate at lower temperatures than Nichrome, are more susceptible to oxidation at high heat without proper encapsulation, and can be significantly more expensive.
- Tungsten and Molybdenum: These refractory metals have extremely high melting points and can withstand very high temperatures. However, they are highly brittle, extremely difficult to work with, and prone to rapid oxidation at high temperatures in air, often requiring inert atmospheres or vacuum for operation. Their high cost also limits their widespread use in general heating applications.
Nichrome Wire vs. Other Common Heating Element Materials
Feature | Nichrome Wire (e.g., 80/20) | FeCrAl Alloys | Copper / Silver | Carbon Fiber | Tungsten / Molybdenum |
---|---|---|---|---|---|
Primary Advantage | Balanced performance: High resistivity, excellent oxidation resistance, good ductility, cost-effective. | Higher max operating temp, good oxidation resistance. | Excellent electrical conductivity. | Rapid heating, flexible, lightweight. | Extremely high melting points. |
Resistivity | High, ideal for heat generation. | High, similar to Nichrome. | Very low, poor for heat generation. | High, good for heat generation. | High. |
Max Operating Temp | ~1200°C (2190°F) | ~1400°C (2550°F) (higher than Nichrome) | ~100-200°C (low) | ~200-500°C (lower than metals) | ~2500°C+ (very high) |
Oxidation Resistance | Excellent (forms stable Cr₂O₃ layer). | Excellent (forms stable Al₂O₃ layer). | Poor (burns in air at high temp unless encapsulated). | Poor (burns in air at high temp unless encapsulated). | Very poor (oxidizes rapidly in air, requires inert atm/vacuum). |
Ductility / Workability | Good (easy to form, draw, weld). | More brittle, harder to form, especially after use. | Excellent. | Good flexibility, but brittle under impact. | Very brittle, extremely difficult to work with. |
Cost | Moderate, good cost-effectiveness. | Moderate to high. | Variable, but low resistivity makes them inefficient for heating. | High. | Very high. |
Common Applications | Toasters, ovens, kilns, lab equipment, industrial heaters, hair dryers. | High-temperature furnaces, industrial heating. | Wiring, electrical contacts, non-heating conductors. | Infrared heaters, wearable tech, specialized heating. | Vacuum furnaces, lamp filaments, X-ray targets. |
Note: Values are approximate and can vary based on specific alloy composition, purity, and manufacturing processes. This table provides a general comparison for common heating element considerations.
In essence, Nichrome strikes a superior balance of performance, workability, and cost-effectiveness, making it a versatile and reliable choice for the vast majority of electric heating applications.
---Widespread Applications of Nichrome Wire
Due to its outstanding properties, Nichrome wire is ubiquitous in a vast array of heating applications across numerous industries:
- Home Appliances: It's the heating element you rely on daily in electric toasters, hair dryers, electric ovens, electric stoves, electric kettles, and even some space heaters. Its rapid heating and durability are key here.
- Laboratory Equipment: Precise heating is crucial for laboratories. Nichrome wire is used in lab ovens, incubators, and heating mantles for controlled experiments and sample preparation.
- Industrial Equipment: Nichrome's durability and stable heat output are vital for high-temperature electric furnaces, heat treatment equipment, and hot air circulation systems.
- Medical Devices: Certain medical devices requiring localized heating, such as sterilizers or specialized heating pads, dental alloys, and electrosurgical scalpels, incorporate Nichrome alloy elements.
- Automotive Industry: In automotive applications, Nichrome elements are used for seat heaters, defrosters, exhaust system sensors, and other heater components.
- Resistors and Heating Coils: Beyond just heating elements, Nichrome is also used in the manufacturing of precision resistors that require stable temperature resistance, as well as various types of heating coils for custom applications.
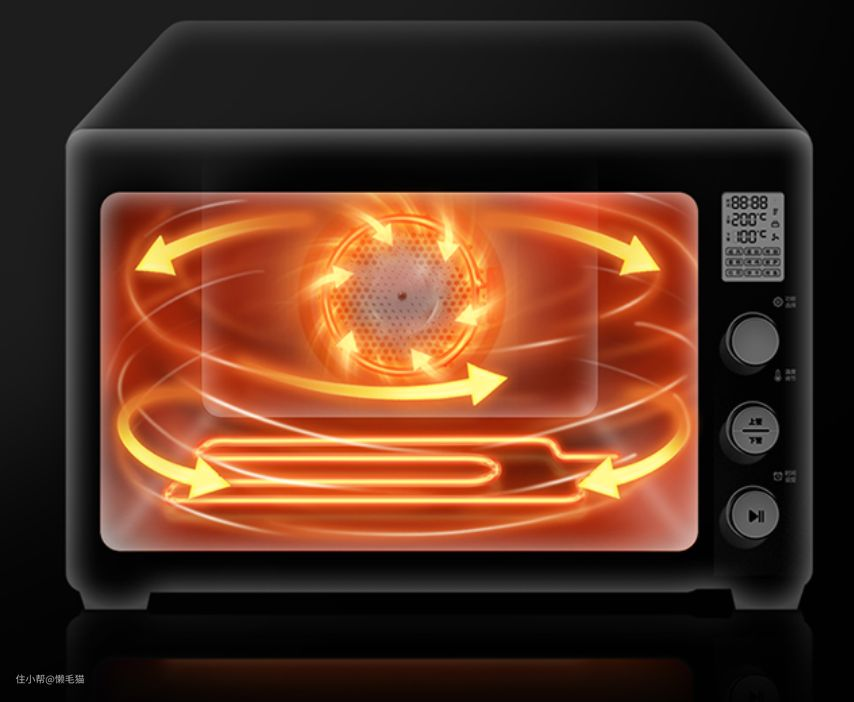
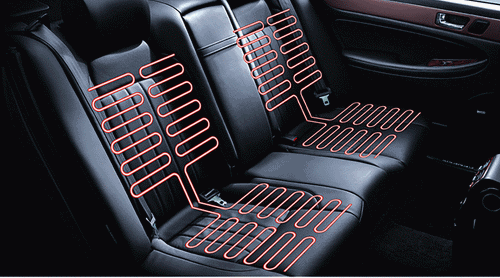
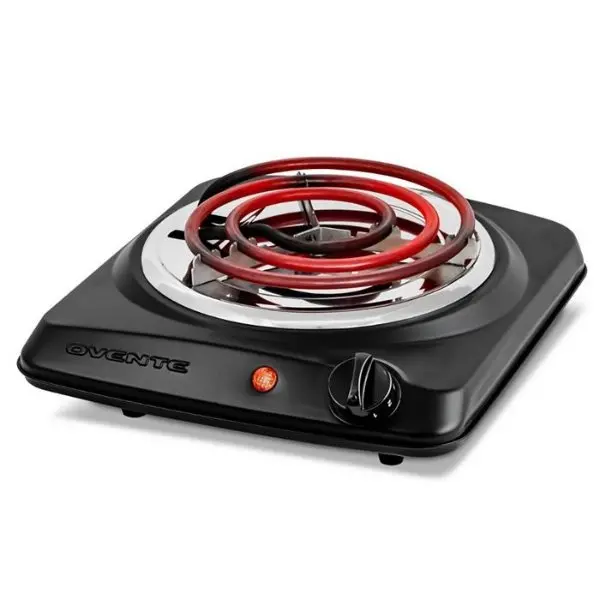

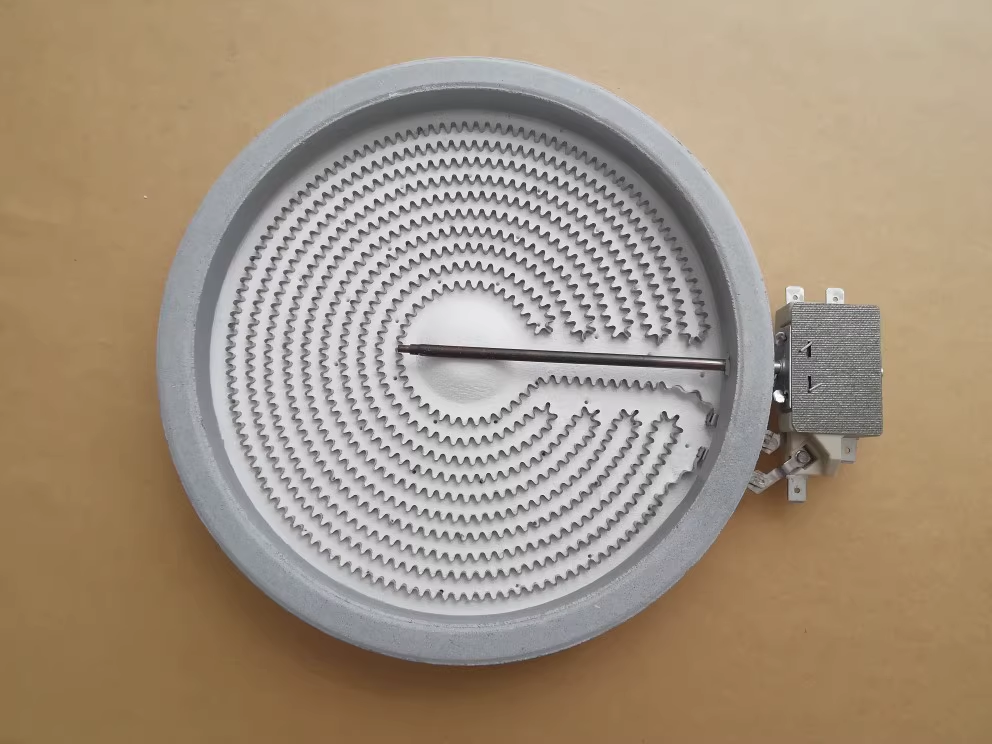

Frequently Asked Questions About Nichrome Wire
Nichrome 80/20, the most common type, typically has a maximum operating temperature of around 1200°C (2190°F). However, specific limits can vary slightly based on the exact alloy composition, wire gauge, and operating environment.
The lifespan of Nichrome wire varies significantly depending on operating temperature, duty cycle (how often it's heated and cooled), atmospheric conditions, and the quality of the wire itself. With proper use and suitable conditions, Nichrome elements can last for many years, thanks to their excellent oxidation resistance and stable properties.
Yes, Nichrome wire is generally considered safe for use in food-related appliances like toasters and ovens. When heated, it forms a stable chromium oxide layer that is inert and does not typically leach harmful substances. However, direct contact with food is usually avoided, and the element is often enclosed or part of a larger heating system.
The most common Nichrome alloys are Nichrome 80/20 (80% Nickel, 20% Chromium) and Nichrome 60 (60% Nickel, 16% Chromium, with some Iron). Nichrome 80/20 is preferred for higher temperatures and longer life, while Nichrome 60 offers a good balance of properties for lower to medium temperature applications.
While minor repairs or splicing are technically possible, it's generally not recommended for critical heating elements, as it can compromise the element's integrity, resistance uniformity, and lifespan. For safety and optimal performance, replacing a damaged heating element is usually the best approach.
Ready to elevate your heating applications?
Contact us today to discuss your specific needs and discover how our high-quality Nichrome wire can provide the perfect heating solution!
Get a Quote